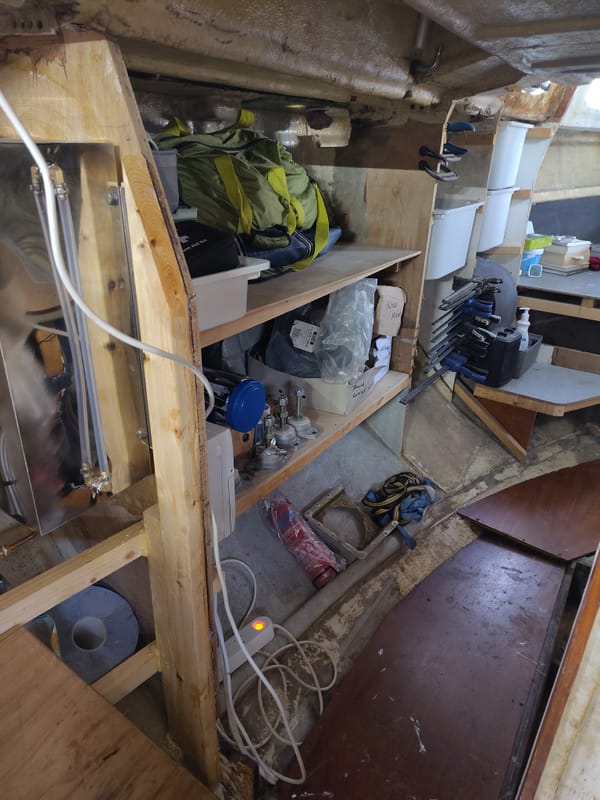
Preparing to move aboard
Acting now to avoid chaos for moving onboard day.
Acting now to avoid chaos for moving onboard day.
So this blog is no longer on Wordpress.com We are now hosted by Magicpages.co using Ghost. Nearly all the original content has been transferred. The only gap I know of at the moment is that the old comments are no longer visible, but I hope to bring them
Jane has finished the first 8 chainplate loops in 12mm dyneema for the main mast (we don't need one for the forestay and the inner forestay will be different). Plus she has finished 3.5 of the 4 lower shrouds (also 12mm dyneema). So we are back to
For once a title like this is not exaggeration and it's not click bait. We are very close to moving to love (nope, I'm not going to correct that typo ;) ) on the boat full-time (current expectation is for 5 years). Jane finished her job at the
Due to a strong, cold North Easterly blowing straight at our companionway we didn't feel like working with the main hatch open all day. Instead, we collected some stuff from our Storage Container. Then Jane started working on the first Dyneema Chainplate Loop for the main mast. Certainly
We haven't been blogging or videoing much recently. That's mainly because we are rushed for time. We will be moving aboard at the end of July and there is a lot to be done: * Boat interior as finished as possible so we are not trying to
It has taken me forever to sort this out. However, it has suddenly come to together very neatly and quickly. With two separate boxes we have 5G and 2.4G Wifi networks on the boat that we can connect to an external WiFi network. Digital Yacht WL510 We have had
This week we have been working on the forecabin (well we also finished the starboard knees for the main mast cap shroud and have been waterproofing the mizzen dyneema chainplate loops). Lots of posts with pictures on Mastodon. This is what we have been doing today (no login required, just
Knees This last weekend we have finished the knees on the starboard side for the main mast cap shroud. We are not going to win any prizes for beauty ;-) But this is so much stronger (remember the original single knee on the starboard side only came down to the
Today we are refitting the original companionway steps. We have been through a few iterations on how to do this as we need them to be removable to give us access to the batteries. In the end we have removed the plywood lining and are fitting two horizontals. A third
Recent events have led us to a significant acceleration this week. Also we now have more than 3.5x more followers of SustainableSailing on Mastodon (https://mas.to/@SustainableSailing) than on Facebook. So we have decided for ethical and health reasons to move faster to get away from the platforms
[Update] The conclusion that we have come to is that we should not compromise. Instead we are going to be doubling down on leaving all the Billionaire controlled social media sites that profit from our personal data, track us everywhere and exploit their workers. So the affiliate links and all